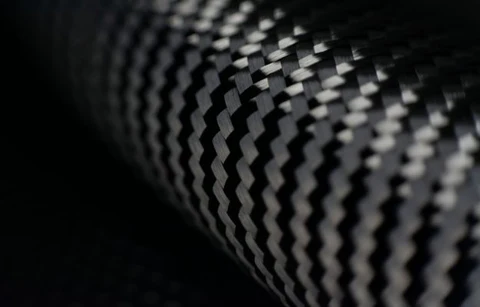
- Introduction
- Definition of Carbon Fiber
- Overview of Its Strength
- Importance of Strength in Various Applications
- The Molecular Structure of Carbon Fiber
- Atomic Bonding in Carbon Atoms
- The Role of Carbon-Carbon Bonds
- The Importance of Crystallinity
- Properties of Carbon Fiber
- Lightweight and Strength: The Fundamental Tradeoff
- Tensile Strength vs. Yield Strength
- Fatigue Resistance and Durability
- Corrosion and Environmental Resistance
- The Manufacturing Process of Carbon Fiber
- Precursor Materials (Polyacrylonitrile – PAN)
- Stabilization and Carbonization
- Tow and Fiber Formation
- The Role of Heat and Pressure in Strength Development
- The Role of Orientation in Carbon Fiber Strength
- Unidirectional vs. Multidirectional Carbon Fiber
- Fiber Alignment on Mechanical Properties
- Laminate Structure and Its Influence on Strength
- Carbon Fiber Composites: Enhancing Strength through Reinforcement
- Matrix Materials (Epoxy, Polyester, etc.)
- Fiber-Matrix Interaction and Its Role in Overall Strength
- Hybrid Composites: Combining Carbon Fiber with Other Materials
- The Role of Carbon Fiber in Different Industries
- Aerospace Industry: Lightweight, Strong, and Safe
- Automotive Industry: Performance and Safety Enhancements
- Sports Equipment and Consumer Goods
- Comparing Carbon Fiber with Other Materials
- Carbon Fiber vs. Steel: Why Carbon Fiber is Stronger in Many Cases
- Carbon Fiber vs. Aluminum: Weight and Strength Considerations
- Other Composite Materials
- Limitations and Challenges
- Brittleness vs. Ductility
- Challenges in Manufacturing and Cost
- Environmental and Recycling
- Conclusion
- Summary of Why Carbon Fiber is Strong
- Future Developments and Potential for Even Greater Strength
- The Role of Carbon Fiber in Advancing Technology
1. Introduction
Definition of Carbon Fiber
Carbon fiber is a material made primarily of carbon atoms arranged in a crystalline structure. The fibers themselves are extremely thin, with diameters typically ranging from 5 to 10 micrometers. Carbon fiber is renowned for its high strength-to-weight ratio, meaning it is incredibly strong yet much lighter than metals like steel or aluminum. This property makes it a preferred material in industries such as aerospace, automotive, sports.
Overview of Its Strength
The strength of carbon fiber is one of its most significant properties. Carbon fiber is not only lightweight but also incredibly strong, making it ideal for applications where structural integrity and durability are critical. This combination of properties sets carbon fiber apart from traditional materials, providing high performance in demanding environments.
Importance of Strength in Various Applications
From aerospace to automotive and sports equipment, carbon fiber’s strength is a key reason for its widespread adoption. Its use allows for the creation of structures that are both lightweight and highly durable, which in turn improves performance, safety, and longevity. The material’s ability to withstand stress and fatigue also makes it ideal for high-performance applications where materials need to maintain structural integrity under extreme conditions.
2. The Molecular Structure of Carbon Fiber
Atomic Bonding in Carbon Atoms
The high strength of carbon fiber is rooted in its molecular structure. Carbon atoms bond with one another to form long, linear chains. These chains are arranged in a highly organized manner, contributing to the fiber’s exceptional tensile strength.
Each carbon atom in the chain forms a covalent bond with its neighboring carbon atoms, creating a strong bond that resists breaking under tension. This bond arrangement gives carbon fiber its characteristic strength and stiffness.
The Role of Carbon-Carbon Bonds
In carbon fiber, the carbon-carbon bonds within the molecular structure are exceptionally strong. These bonds, along with the unique alignment of the carbon atoms, contribute to the overall strength of the material. The strong bond between atoms in the fiber results in a highly rigid structure, capable of withstanding significant mechanical stress without deforming or breaking.
The Importance of Crystallinity
The crystalline structure of carbon fiber is another factor that contributes to its strength. The degree of crystallinity refers to the extent to which the carbon atoms are arranged in a regular, repeating pattern. The higher the degree of crystallinity, the stronger and more rigid the material becomes. A highly crystalline structure enhances the fiber’s ability to resist deformation under stress, which is critical for applications that require superior strength.
3. Properties of Carbon Fiber
Lightweight and Strength: The Fundamental Tradeoff
One of the most significant advantages of carbon fiber is its high strength-to-weight ratio. The material is incredibly strong for its weight, making it an ideal choice for applications that require strength without adding significant weight. This property is especially important in industries such as aerospace, where reducing weight is essential for improving fuel efficiency and performance.
Tensile Strength vs. Yield Strength
Tensile strength is the maximum amount of tensile stress that a material can withstand before breaking, while yield strength refers to the point at which a material begins to deform permanently under stress. Carbon fiber’s high tensile strength allows it to bear heavy loads without breaking, while its high yield strength ensures that it maintains its shape and structural integrity under stress.
Fatigue Resistance and Durability
Carbon fiber is resistant to fatigue, meaning it can endure repeated stress cycles without failing. This is a crucial property for components that are subject to constant loading and unloading, such as aircraft wings or automobile body panels. Additionally, carbon fiber has excellent durability, maintaining its strength and performance over long periods, even under harsh environmental conditions.
Corrosion and Environmental Resistance
Unlike metals such as steel, carbon fiber is resistant to corrosion caused by moisture, salt, and other environmental factors. This resistance to corrosion makes carbon fiber particularly useful in industries where components are exposed to challenging conditions, such as aerospace, automotive, and marine applications.
4. The Manufacturing Process of Carbon Fiber
Precursor Materials (Polyacrylonitrile – PAN)
The manufacturing process of carbon fiber begins with the selection of precursor materials. The most common precursor for carbon fiber is polyacrylonitrile (PAN), a polymer that contains a high percentage of carbon. PAN fibers are processed through a series of steps to convert them into carbon fiber.
Stabilization and Carbonization
Once the PAN fibers are produced, they undergo a process called stabilization, where the fibers are heated in air to form a thermally stable structure. After stabilization, the fibers undergo carbonization, where they are heated to very high temperatures (typically between 1,000 and 3,000 degrees Celsius) in an inert atmosphere, causing the carbon atoms to bond together more tightly and forming the carbon fiber structure.
Tow and Fiber Formation
The carbon fiber is then spun into tows—bundles of individual fibers that can be woven into fabrics or used in other manufacturing processes. The fibers are formed into various diameters depending on the intended application, with thinner fibers providing greater flexibility and thicker fibers offering higher strength.
The Role of Heat and Pressure in Strength Development
The carbonization process, combined with the application of heat and pressure during manufacturing, results in the high strength of carbon fiber. The heat causes the carbon atoms to bond more strongly, increasing the strength of the final product. Pressure is applied during the molding or weaving process to ensure that the fibers align correctly, further enhancing the material’s strength.
5. The Role of Orientation in Carbon Fiber Strength
Unidirectional vs. Multidirectional Carbon Fiber
The orientation of the carbon fibers significantly affects their strength. Unidirectional carbon fiber, where the fibers are aligned in a single direction, provides maximum strength along that direction. On the other hand, multidirectional carbon fiber, where fibers are woven in different directions, provides strength in multiple directions but may be slightly less strong in any one direction.
Fiber Alignment on Mechanical Properties
The alignment of the carbon fibers directly the material’s mechanical properties. When the fibers are aligned in the direction of the load, the material exhibits exceptional strength and stiffness. This is why unidirectional carbon fiber is often used in high-performance applications where strength in a specific direction is critical, such as in aerospace and automotive components.
Laminate Structure and Its Influence on Strength
In many applications, carbon fiber is used in laminate structures, where layers of unidirectional carbon fiber are stacked at different angles to create a composite material. This arrangement allows the material to resist stress from multiple directions, making it stronger and more versatile.
6. Carbon Fiber Composites: Enhancing Strength through Reinforcement
Matrix Materials (Epoxy, Polyester, etc.)
In many applications, carbon fiber is combined with a matrix material, such as epoxy resin or polyester, to form a composite material. The matrix holds the carbon fibers together and helps distribute the stress across the
fiber network. The strength of the composite is enhanced by the combination of the strong carbon fibers and the durable matrix material.
Fiber-Matrix Interaction and Its Role in Overall Strength
The strength of a carbon fiber composite depends not only on the carbon fiber itself but also on how well the fiber and matrix materials interact. The better the bonding between the fibers and the matrix, the stronger the composite will be. This is why selecting the right matrix material and ensuring proper curing are critical steps in the manufacturing process.
Hybrid Composites: Combining Carbon Fiber with Other Materials
In some applications, carbon fiber is combined with other materials, such as glass fiber or Kevlar, to create hybrid composites. These composites can offer enhanced performance characteristics, such as increased toughness or improved resistance, while still retaining the high strength and light weight of carbon fiber.
Conclusion
In conclusion, carbon fiber has high strength due to its unique molecular structure, the strength of carbon-carbon bonds, and the crystalline arrangement of its atoms. Its high strength-to-weight ratio, coupled with its resistance to fatigue, corrosion, and environmental degradation, makes it a material of choice in many industries. By understanding the manufacturing process, fiber orientation, and matrix reinforcement, we can appreciate why carbon fiber is considered one of the strongest materials available. As research and development in material science continue, the strength of carbon fiber is expected to improve, opening new possibilities for its use in even more demanding applications.