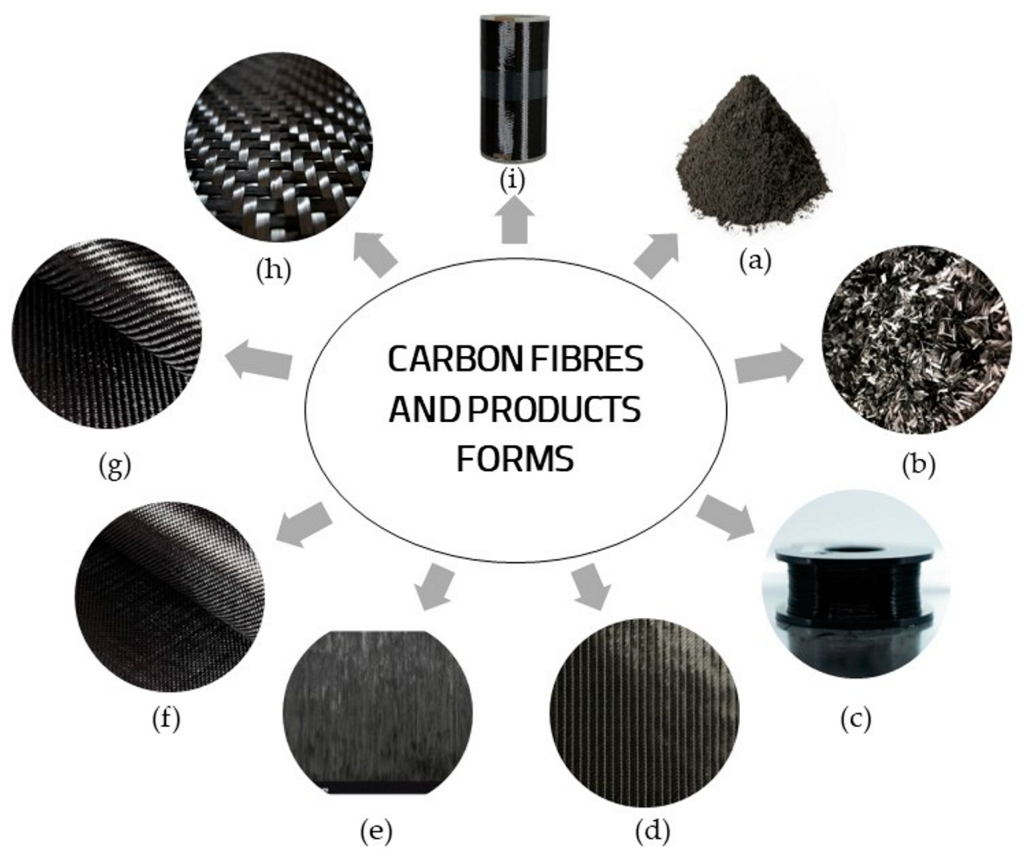
Carbon fiber is a versatile material celebrated for its exceptional strength-to-weight ratio, corrosion resistance, and thermal stability. It fi.nds applications in industries ranging from aerospace to sports equipment, and its properties can be tailored to specific needs. Understanding the various types of carbon fiber and their unique characteristics is essential for optimizing their use. This article explores the main categories of carbon fiber, highlighting their distinct features, manufacturing processes, and applications.
1. Types of Carbon Fiber Based on Precursor Material
1.1 PAN-Based Carbon Fiber
- Definition: Derived from polyacrylonitrile (PAN), this is the most commonly used type of carbon fiber.
- Characteristics:
- High tensile strength and modulus.
- Excellent thermal and chemical resistance.
- Uniform structure, making it ideal for aerospace and automotive applications.
- Applications: Aircraft components, high-performance automotive parts, and sporting goods.
1.2 Pitch-Based Carbon Fiber
- Definition: Made from petroleum or coal tar pitch.
- Characteristics:
- Extremely high modulus and thermal conductivity.
- Brittle compared to PAN-based fibers.
- Superior vibration damping properties.
- Applications: Satellite components, heat exchangers, and thermal management systems.
1.3 Rayon-Based Carbon Fiber
- Definition: Derived from regenerated cellulose fibers, primarily used historically.
- Characteristics:
- Moderate mechanical properties.
- Excellent ablative properties, suitable for high-temperature applications.
- Applications: Rocket nozzles and heat shields.
2. Types of Carbon Fiber Based on Structure
2.1 High-Strength Carbon Fiber
- Definition: Optimized for tensile strength.
- Characteristics:
- High tensile strength (>4000 MPa).
- Moderate modulus.
- Applications: Aerospace, sports equipment, and pressure vessels.
2.2 High-Modulus Carbon Fiber
- Definition: Optimized for stiffness.
- Characteristics:
- Extremely high modulus (>300 GPa).
- Lower tensile strength compared to high-strength fibers.
- Applications: Satellites, robotics, and precision instruments.
2.3 Intermediate-Modulus Carbon Fiber
- Definition: Balances strength and stiffness.
- Characteristics:
- Tensile strength between 3000-4000 MPa.
- Modulus between 200-300 GPa.
- Applications: General-purpose industrial and automotive components.
2.4 Ultra-High-Modulus Carbon Fiber
- Definition: Designed for extreme stiffness.
- Characteristics:
- Modulus exceeding 600 GPa.
- Limited tensile strength and flexibility.
- Applications: Specialized aerospace and scientific equipment.
3. Types of Carbon Fiber Based on Form
3.1 Continuous Fiber
- Definition: Long, unbroken strands of carbon fiber.
- Characteristics:
- Maximum strength and stiffness.
- Requires careful handling and application.
- Applications: Aerospace, wind turbines, and structural beams.
3.2 Chopped Fiber
- Definition: Short segments of carbon fiber.
- Characteristics:
- Easy to mix with other materials.
- Lower strength compared to continuous fibers.
- Applications: Injection molding, thermoplastics, and non-structural parts.
3.3 Woven Fabrics
- Definition: Carbon fibers interwoven into fabrics.
- Characteristics:
- Enhanced durability and flexibility.
- Available in different weave patterns (plain, twill, etc.).
- Applications: Automotive interiors, protective gear, and marine components.
4. Characteristics of Carbon Fiber Categories
4.1 Mechanical Properties
- High tensile strength and stiffness.
- Lightweight, reducing overall structural mass.
- Low thermal expansion, ensuring dimensional stability.
4.2 Thermal and Electrical Properties
- Excellent thermal conductivity in certain types (e.g., pitch-based fibers).
- High electrical conductivity, making it suitable for EMI shielding.
4.3 Chemical Resistance
- Corrosion-resistant to acids, alkalis, and solvents.
- Ideal for use in harsh environments.
4.4 Aesthetic and Design Flexibility
- Sleek appearance for visible applications.
- Customizable forms for intricate designs.
5. Manufacturing Processes
5.1 Precursor Material Selection
- Determines final properties like strength, modulus, and thermal stability.
- PAN-based precursors dominate the market due to their versatility.
5.2 Stabilization and Carbonization
- Stabilization involves heating fibers to 200–300°C.
- Carbonization at 1000–3000°C removes non-carbon elements, increasing purity.
5.3 Surface Treatment and Sizing
- Enhances fiber bonding with resins.
- Sizing agents improve compatibility with composite matrices.
6. Emerging Trends and Innovations
6.1 Hybrid Composites
- Combining carbon fibers with other materials for cost-effective solutions.
- Improved performance tailored to specific applications.
6.2 Sustainable Carbon Fiber
- Development of bio-based precursors.
- Recycling initiatives for end-of-life composites.
6.3 Additive Manufacturing
- Integration of carbon fibers in 3D printing for lightweight, strong components.
- Enabling rapid prototyping and customization.
Conclusion
The classification of carbon fiber into various categories based on precursor materials, structure, and form highlights its adaptability to a wide range of applications. Each type offers unique characteristics, making carbon fiber a critical material in industries seeking high performance, sustainability, and design innovation. As research and development continue to drive advancements, the potential of carbon fiber will only expand, solidifying its role in the future of material science and engineering.